As part of our commitment to providing high quality technical products to our customers, Dura Magnetics has established a formal product realization process base on the Advanced Product Quality Planning (APQP) process.
An established product realization process is a requirement for AS9100D certification for production of aerospace products and components. Although product realization is only a small part of this certification, it is a critical component of the design and development of new parts. This process includes a positive feedback loop of testing and refining that ensures the quality and design of the magnet as well as the larger assembly of which it will be a component.
Dura’s APQP process, described below, ensures an effective process, conforming products, and on time deliveries for the aerospace industry at every stage of fabrication.
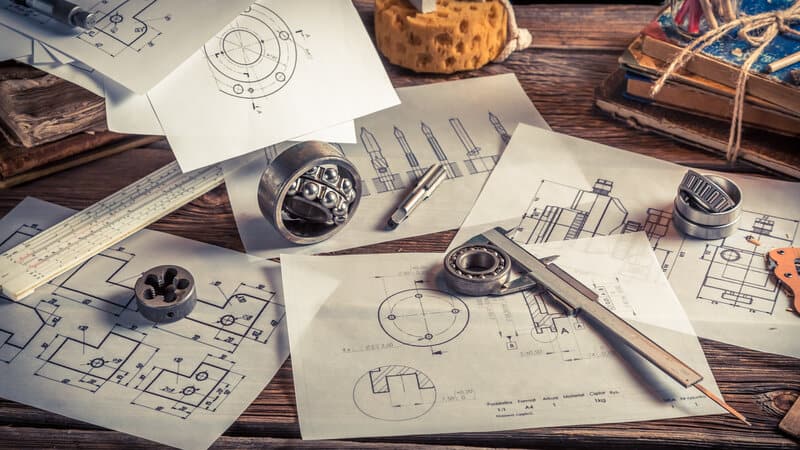
The APQP process
The International Aerospace Quality Group has adopted a specific standard, the AS9145, with the intention of standardizing the product development process. This standard integrates requirements for aviation, aerospace, and defense applications. Part of standardizing product development is the adoption of an Advanced Product Quality Planning process; another separate element is the production part approval process methodology.
APQP has five phases, starting with product conception and extending throughout the development cycle. Each phase is intended to ensure the product meets customer product expectations. The overall process allows for flow down of standards, the appropriate allocation of resources, as well as clearly defined scope and responsibilities.
With the APQP process in place, targets are established early. These include:
- Reliability
- Safety
- Quality
- Service life
Essentially, APQP is a formalization of the manufacturing process to assure the aerospace customer is provided exactly what they commissioned, and to test repeatedly and verifiably whether the vendor can deliver the specified quality and quantity of that product as established in the original planning stage.
This process is designed to ensure quality throughout the entire supply chain to prevent non-conforming parts from going into the aircraft. There is, of course, no room for error; therefore, every component on the aircraft must be certified.
Because Dura Magnetics creates magnets for a variety of aerospace applications, we are well-versed in the AQPQ process. For example, we have provided the magnet used in an aircraft braking systems as well as one used in a flight attendant’s handset. Each and every component in the supply chain must be rigorously tested and approved before it can be installed, including components from Dura Magnetics. Here is how it works:
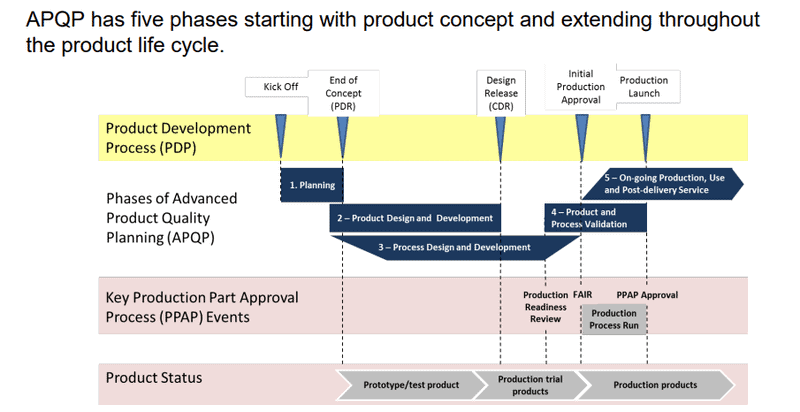
APQP 1: Objective
The first phase of APQP establishes the objective of the endeavor: What is to be achieved, fabricated, or produced. Phase 1 captures customer inputs, applicable regulatory information, technical requirements, and strategy to establish high-level targets regarding cost and capability.
In this phase, Dura establishes what we will be delivering to the customer. That may include, among many other factors:
- Capabilities and technical qualities.
- The required level of certification.
- Regulatory compliance such as DFARS and ITAR.
After the product concept and preliminary fulfillment plan are finalized, a quote is delivere based on estimates and the contract is drawn up and signed.
APQP 2: Specification
The second phase of the APQP process is the product design and development phase. During this step, risk is analyzed and we apply the technical and cost requirements to create a validated product design using prototype parts in testing environments. This verifies the product can be produced as described in a manner that accomplishes the stated targets.
At Dura, we generate a beta engineering drawing, design record, and bill of materials for customer approval. The customer reviews the formal drawing, and both sides agree as to what will be created.
APQP 3: Process
The third phase of APQP determines the repeatable process that will be implemented, demonstrating control and consistent quality. It is impermissible for a process to be inconsistent; phase 3 ensures and verifies that the process works 100% of the time.
For example, in the manufacturing of a particular magnet, a capability study of up to 50 or 100 parts may be completed, determining how best to grind, rack, and deburr the part. We establish the number of hours the product will be on each machine and determine the production process necessary to achieve consistent results under the technical specifications created in APQP2. We also verify that the process can produce parts at the specified customer demand rate. The result requires iterative and incremental refinement.
APQP 4: Product and Process Validation
The fourth phase of APQP verifies the fulfillment process is in control at the expected customer demand rates. At this phase, we have established a process for creating a product; and it is substantiated to be in control with initial process capability studies. This proof stage validates the final production process and demonstrates the product will meet the established requirements. Statistical analysis ensures that the process control is comprehensive and constant.
The output of this stage is Process Validation and customer approved PPAP and FAIR submissions.
APQP 5: On-going Production
Once the customer has accepted the FAIR and or PPAP submission, we are ready to build production quantities using the procedures and documentation developed during the APQP process. We execute the production order according to this process established during the first four phases of the product quality plan.
We carry out the production of the part according to customer timing; if issues arise (a formal nonconformance), we respond with corrective action and show the client how we have addressed the root cause of the issue.
All five phases must be complete to take an aerospace part from conception to production and deliver the final, certified product to the customer.
Your Aerospace Partner
Producing aerospace products and components requires rigorous adherence to strict quality controls and standardization of applied process requirements. Dura Magnetics is AS9100D certified to execute an APQP plan that meets rigid AS requirements as specified by the International Aerospace Quality Group.
You can be assured of a rock-solid development process when partnering with Dura Magnetics. As experts in highly technical fabrication, we engage and work with aerospace clients every step of the way, along with outstanding, personalized communication — our specialty.
Contact us to discover how Dura Magnetics can assist your organization with its magnetic fabrication needs in aerospace, aviation, or defense applications. Our magnet specialists are ready to help.