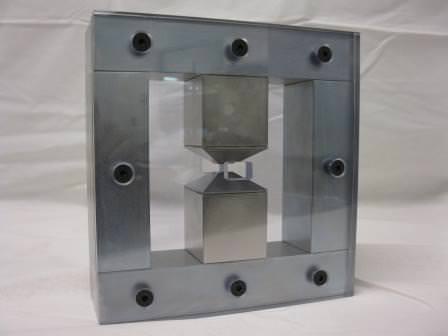
Permanent Magnet Dipoles, in the industrial sense, are two pole units used to create intense and often uniform magnetic fields.
In the simplest form, a dipole is a pair of magnets separated by a gap. The gap is where the useful field resides. The magnets are commonly used in conjunction with a yoke or return path. The return path / yoke is usually comprised of mild steel and is integral to the magnetic circuit design. The metal elements offer an increase in usable field in the gap by magnetic induction as well as routing flux. They also allow for a means to secure the system.
A dipole may be required to deliver a high field density with a particular direction, a very homogeneous field, or both. To support both deliverables, high field density, and uniformity, pole caps can be applied. Often, the pole caps are fabricated from high saturation and/or high permeability alloys.
Typical Applications:
- Small Particle Separation (Micro – Nano)
- Charge Particle Biasing
- Magnetic Annealing (Thin Films, Alloy Ribbon and Amorphous Cores)
- Probe Calibration
- Nuclear Magnetic Resonance (MR) (MRI)
- Ferrous Product alignment
Key Considerations:
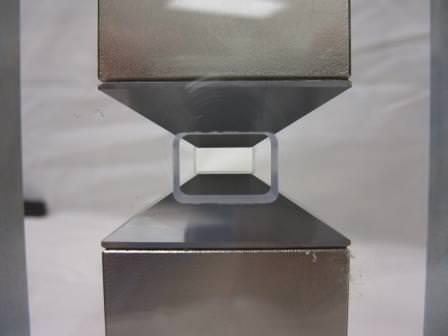
The typical limitation of a dipole’s field density and homogeneity is the effective gap between the magnets. The larger the gap, more and more resources are needed to create a highly dense and / or uniform magnetic field.
Another first order design reference is the desired field density in the gap in relation to the magnet’s Magnetic Induction (Br). For small gaps, near 80- 90% Br is generally easily attained with simple structures. Operating at or above this Br requires more material and enhanced designs. As the gap increases from a few millimeters to several centimeters, more and more magnet volume is required.
Operating Environment Considerations:
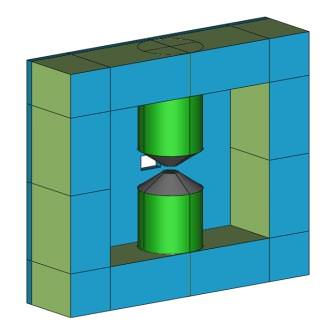
The force of attraction between the magnet poles is very large in even small table top dipoles. The acceleration of ferrous object into the dipole also presents some challenges. It is imperative that operators and technicians are aware of the hazards when working around permanent magnet dipoles. Operator protection guarding is a key design variable.
Dipoles operating in higher temperature environments are subject to a net field degradation and possibly an irreversible field loss. The operating temperature of the dipole is a key design variable and must be accounted for.
Dipoles, as with most magnets, will not tolerate operational environments where gasses and liquids will promote corrosion. The presence of corroding gasses and liquids is a key design variable.
Dipoles can be designed to limit outgassing, but typically they are used external to vacuum elements.
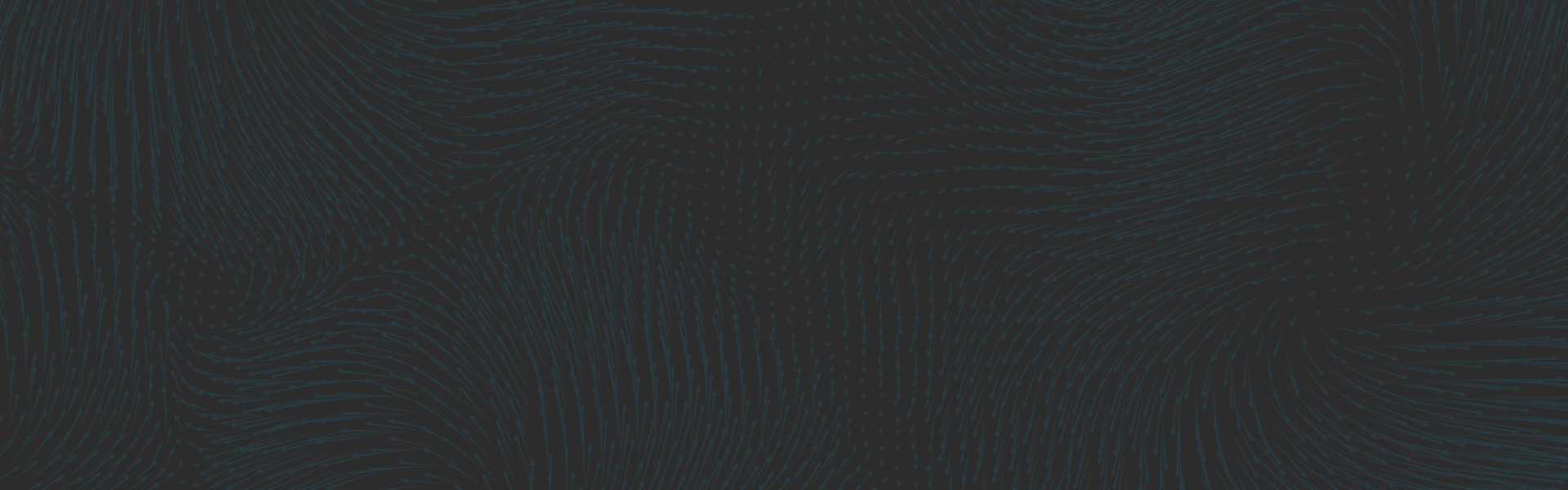
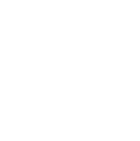
ITAR Registered & Compliant
We are registered and compliant with the International Traffic in Arms Regulations (ITAR). This qualifies us to work with items listed on the United States Munitions List (USML). We are also ITAR registered with the Directorate of Defense Trade Controls (DDTC).