Below is a list of commonly specified features which are typically not applicable to magnet materials. These features can be produced, but may add unnecessary cost and are usually specified as a drawing “title-block default” or by a designer with limited knowledge of magnetic material.
The professionals at Dura can work with your design team to ensure that specifications reflect application requirements without adding unnecessary cost or creating a non-conforming condition.
- Surface Finish Requirements—When necessary, magnet material is typically ground. When not required for dimensional control, the alloy is left “as-cast” or “as sintered.” Should a surface finish specification be specified as a default in the drawing title block, it may impose a need for additional fabrication which then will result in unnecessary cost.
- Edge Break Requirements–Magnets are very “hard” and brittle, so most edge break features are applied by abrasive tumbling or grinding. This process is not as simple as de-burring conventional materials. “Edge-break Specification” is a default often represented in the drawing’s title-block and the designer is may not be aware of the cost implications regarding a tight tolerance edge-break feature.
- Blind Hole / Counter-Sink Features–Because magnets are very hard and brittle, these features are ground or produced with an EDM. (The resistivity of magnet alloy results in long burn times and tapers.) These features can be fabricated, but are more expensive than producing blind hole or counter-sink features in common commercially available materials.
- Retaining Shoulder, Taper Features, and Threads–These design elements can be produced by grinding, but they come with a high cost. Dura’s experts can recommend other more cost effective retaining options that can reduce your manufacturing costs.
- ASTM Plating Specifications— Although the applied process may be similar, most plated magnets are not certified to a particular ASTM plating specification. The application of metals to the surface of magnet material is quite challenging. Dura is one of only a few companies worldwide that have the knowledge and expertise needed for such applications. Typically Dura can supply the magnetic solution in accordance with an agreed upon performance-level traceable to an ASTM environmental testing specification. (Typically ASTM B117 – Salt Spray)
- Plating Thickness— This design consideration is dictated by the plating process and optimized for the alloy and not necessarily for achieving thickness. Unlike typical metal plating options for commercial materials, Service Codes (SC) indicating performance in various environments are not available. Additionally, magnets should not be designed to operate in aggressive operational environments, regardless of the plating. Typically Dura can supply a magnetic solution in accordance with an agreed upon performance level that is traceable to an ASTM environmental testing specification. (Typically ASTM B117 – Salt Spray)
- Specification of Magnets as Structural Elements–Magnet alloys will tolerate high compressive loads, but they are very prone to fracturing when stressed in tensile or flexed. It is important to note that magnetic material should not be used as a structural design element.
Should you or your company have need for further information regarding cost effective solutions, please don’t hesitate to contact Dura’s team of experts.
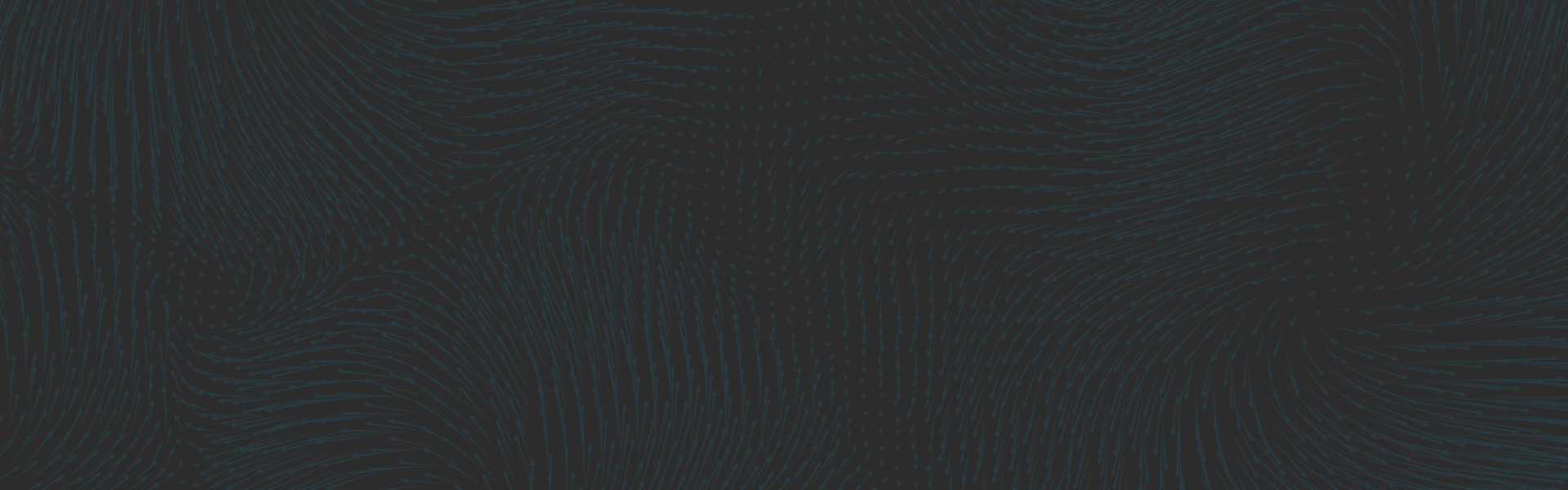
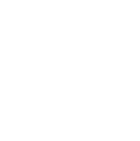
ITAR Registered & Compliant
We are registered and compliant with the International Traffic in Arms Regulations (ITAR). This qualifies us to work with items listed on the United States Munitions List (USML). We are also ITAR registered with the Directorate of Defense Trade Controls (DDTC).