There are limits to how much induced magnetism is possible in different materials and similar workpieces of varying size, shape, and configuration. The principle of magnetic saturation observes that there is a point of diminishing returns at which attempting more externally applied magnetic field (H) will give rise to no additional magnetic induction (B). Increasing the thickness of a workpiece is generally beneficial. However, these changes will likely impact cost, mass, and possibly ease of manufacturing. It is therefore beneficial to understand and control for the magnetic saturation of materials during the design stage.
In a previous blog posting about magnetic permeability, we discussed why ferrous materials are attracted to a magnet: the magnet’s magnetic field induces a magnetic field into the steel and the fields interact, such that, the magnet and the steel attract.
Magnetic permeability is the aspect of a material which illustrates the degree a material is attracted to a magnet (from an engineering standpoint, magnetic permeability is a material’s ability to support an internal magnetic field induced by an external magnetic field). We learned in the “Magnetic Permeability” blog posting that the permeability of a material is dependent upon several factors and that one of these factors is the applied drive-field strength presented to the steel.
The ability to induce a pole in a material is not infinite and is limited as a material’s magnetic permeability decreases. When the magnetic permeability of a “workpiece” drops to “1” the material is said to be saturated. This is the point where no more external applied field (H) will give rise to any additional magnetic induction (B). No additional magnetic induction, therefore no additional attractive force; the system has reached its maximum limit and it is said to be at saturation.
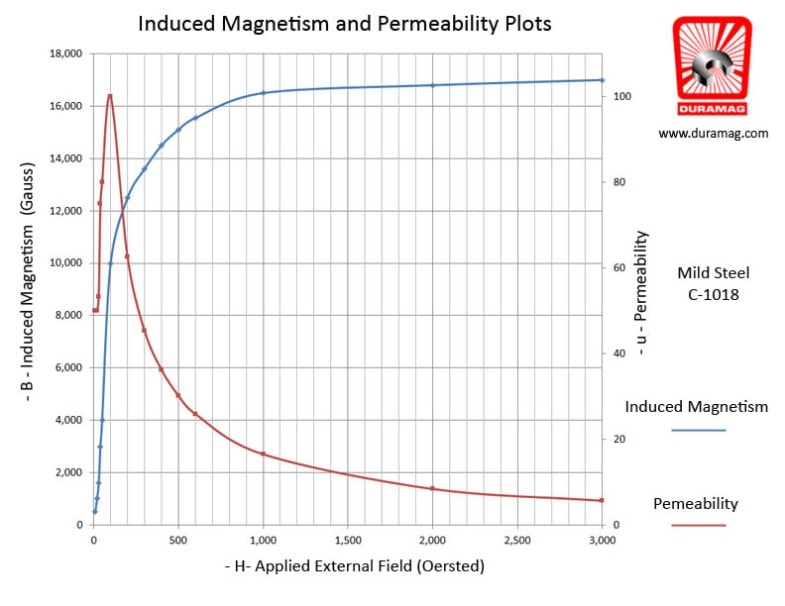
Figure 1: A plot depicting the induced magnetism and permeability in mild steel, relative to a spectrum of applied field strengths. As the maximum induced magnetism is achieved, the mild steel’s permeability goes to “1” and the slope “flattens” out. At this point the material is “Saturated”
Saturation usually occurs in thinner workpieces where there is less volume of material to act on. Oftentimes, the entire workpiece does not saturate and there is actually a gradient within the workpiece with only portions being driven into saturation. Even though the entire workpiece does not saturate, the force is still limited because the non-saturating areas are not contributing to the attractive force.
Magnetic Saturation: How to Tell if a Magnet is Fully Saturated
Directly measuring the degree of saturation within a material can be difficult as this is an internal phenomenon. There are, however some first order methods which may indicate a system is in saturation. One option is to inspect the non-working face of the workpiece (the face which is opposite of the externally applied magnetic field) and try to observe any field “leaking” through. The degree of the leakage is a good indicator of saturation and suggests the workpiece would benefit from being thicker. The other option is to increase the workpiece’s thickness and see what effect it has. If one doubles the thickness of the workpiece and receives a measurable increase in attractive force, then the original workpiece was saturating, however, there is a point of diminishing returns. Increasing the thickness of a workpiece is generally always beneficial, but it will impact cost, mass, and possibly ease of manufacturing.
In conclusion:
- Saturation can negatively impact a design by lowering the overall magnetic efficiency of the system.
- Saturation of a material can be thought of the limit at which the material can carry magnetic flux. A pipe analogy works well as there is a limit to the volume of material carried by a pipe a there is a limit of magnet field a material can carry.
- There is a limit to how much induced magnetism is possible in a material. When no more internal magnetism can be created within a material, it is said to be saturated.
- Saturation is a fluid condition which is dependent upon the material’s magnetic characteristics and the intensity and direction of the applied magnetic field.
- Thinner workpieces usually suffer from saturation more than thicker workpieces.
- Magnetic saturation in the workpiece limits the effective attractive force between the workpiece and a magnet.
Dura Magnetic is a leading supplier of stock neodymium magnets, ceramic magnets, alnico magnets and samarium cobalt magnets. Our engineers daily help companies develop complex design-for-manufacturability solutions. Our technical expertise is recognized as helping drive decisions that impact cost, product mass, and often ease of manufacturing magnetic assemblies. Please contact us for help with magnetic design or application assistance.